Unleashing Precision and Efficiency: The Rise of Laser Welder Machines
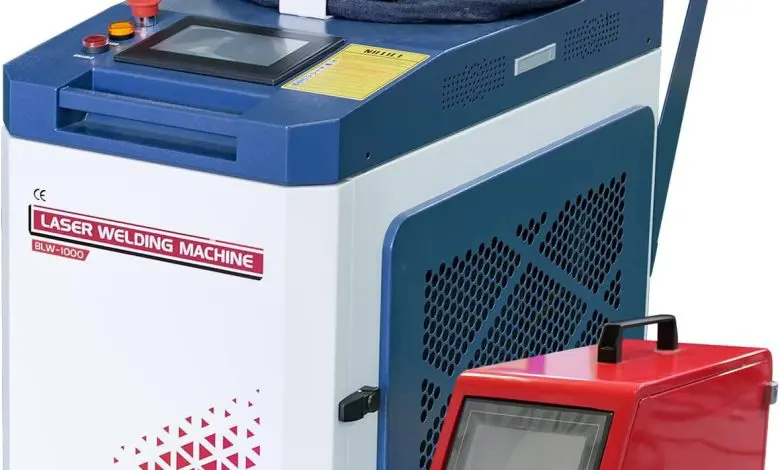
Laser Welder Machines: The evolution of industrial technology has ushered in an era where precision, efficiency, and reliability are not just desired but required. At the forefront of this technological advancement stands the laser welder machine, a marvel of engineering that has transformed manufacturing processes across a myriad of sectors. This blog post explores the essence of laser welding machines, their advantages, applications, and future prospects, highlighting their pivotal role in modern manufacturing.
The Core of Laser Welding Technology
Laser welding employs a highly concentrated light beam as its source of heat to melt and fuse materials together. This light beam, focused to a precise point, allows for unmatched accuracy and control in the welding process. Unlike traditional welding methods, laser welding does not require contact, reducing wear and tear on tools and allowing for the welding of delicate and intricate parts.
Advantages of Laser Welding Machines
Precision and Control: The ability to focus the laser beam to a fine point permits the welding of minute components with high precision. This is crucial in industries where even the slightest error can compromise the integrity of the product.
Versatility: Laser welding machines can work with a wide range of materials, including metals, plastics, and composites. This versatility makes them invaluable to industries such as automotive, aerospace, and electronics, where different materials need to be joined with precision.
Speed and Efficiency: Laser welding is significantly faster than conventional welding methods. The process is automated, leading to increased production speeds and consistent output quality, which, in turn, reduces labor costs and enhances efficiency.
Minimal Heat Impact: The concentrated heat source means that the area affected by heat is minimal, reducing distortion and allowing for the welding of heat-sensitive materials. This characteristic is particularly beneficial in the electronics industry, where components are often delicate.
High-Quality Welds: The precision and control offered by laser welding result in strong, high-quality welds that are consistent and repeatable. This reliability is essential in industries where weld strength and integrity are paramount.
Applications of Laser Welding Machines
Laser welding technology’s flexibility and precision have made it indispensable in numerous fields:
- Automotive Industry: Used for welding components in vehicles, such as gearbox components, engine parts, and batteries. The technology’s precision is critical for ensuring the safety and reliability of automotive parts.
- Medical Devices: Laser welding is used in the fabrication of medical devices, including surgical instruments and implants. Its ability to produce sterile, high-quality welds without contaminating the material is particularly valuable.
- Electronics: In the production of electronic components and circuit boards, laser welding’s minimal heat impact is essential for preserving the integrity of delicate parts.
- Aerospace: The aerospace industry relies on laser welding for the construction of aircraft components. The technology’s ability to produce strong, durable welds in lightweight materials is crucial for maintaining the structural integrity of aerospace vehicles.
The Future of Laser Welding Machines
As industries continue to seek more efficient, reliable. And precise manufacturing methods, the role of laser welding machines is set to expand. Advancements in laser technology, such as the development of fiber lasers, are making laser welding machines more accessible and cost-effective. Moreover, the integration of artificial intelligence and machine learning algorithms is enhancing the automation capabilities of laser welding systems, enabling them to adapt to different materials and welding parameters in real time.
The potential for environmental impact reduction also makes laser welding a technology of the future. With its high efficiency and minimal waste production. It offers a more sustainable alternative to traditional welding methods, aligning with global efforts to reduce industrial carbon footprints.
Conclusion
Laser welding machines represent a significant leap forward in manufacturing technology, offering unmatched precision, efficiency, and versatility. Their impact is evident across various industries, from automotive and aerospace to electronics and medical devices. As technology continues to advance, the capabilities of laser welding machines will only grow. Further solidifying their position as a cornerstone of modern manufacturing processes. The journey of laser welding technology is a testament to human ingenuity’s ability to push the boundaries of what is possible, paving the way for a future. Where precision and efficiency are at the heart of production.