Waterproof Sticker Materials 101: What Lies Beneath the Surface
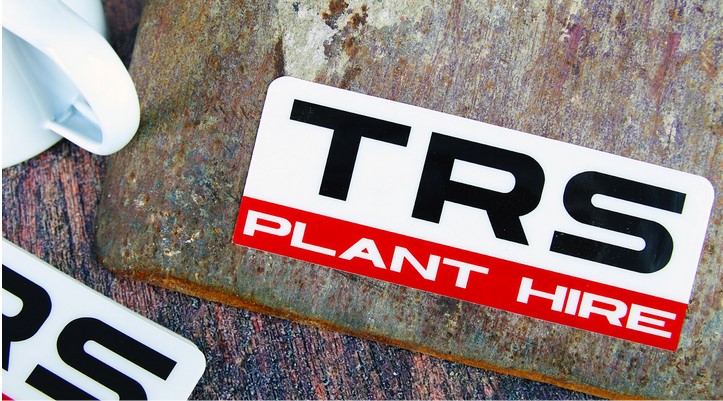
In the fast-paced world where branding is a battlefield, stickers have emerged as the guerrilla marketers’ go-to weapon—the small, unassuming tools that pack a massive perceptual punch. Yet, with the multitude of environments these stickers are exposed to, especially those labeled ‘waterproof’, it is essential for marketers and business owners to understand the constituents of sticker materials and how to test their true durability. For the creators of visual identity, the question then becomes, “How can I trust my stickers will remain steadfast in the face of adversity?”
Below, we’ll explore the answers by dissecting waterproof sticker materials and offering a roadmap for testing their mettle. This guide is a crucial resource for small business owners and marketing professionals who are keen on ensuring their promotional stickers will not only survive but thrive in tough terrains.
The Chemistry of Durable Stickers
The chemistry behind sticker materials is fascinating. Vinyl, for instance, is crafted using ethylene (a component of natural gas) and chlorine (sourced from salt). This results in PVC, or polyvinyl chloride, a versatile plastic with many applications, including sticker production. Other materials like cast vinyl offer enhanced durability due to their manufacturing process, which stretches the material, aligning the molecules and creating a film with enhanced strength and elasticity.
Choosing the Right Material for Your Project
Selecting the proper sticker material is not merely about waterproofing; it’s a delicate balance between durability, cost, and aesthetic appeal. Matte vinyl, for example, is suitable for stickers that need to remain legible in various lighting conditions, while high-gloss vinyl enhances color vibrancy, crucial for catching the eye. Additionally, matte laminate can be added to provide extra protection against scratching, which is beneficial for stickers expected to endure rough handling.
The Five Stages of Water Torture for Stickers
Waterproof is a promise, but promises can be broken. To ensure the stickers will hold up under all circumstances, testing is crucial. Here, we will walk through the five stages of water torture—a metaphorical term used to describe various levels of exposure to water—applied to sticker materials.
Stage One: The Damp Test
In this stage, stickers are placed in a location where they are exposed to mild moisture, such as a room with high humidity or light rain. The goal is to observe if any material begins to curl, peel, or lose adhesive properties.
Stage Two: The Splash Test
For the splash test, stickers are subjected to direct water contact for a short period. This mimics situations where the sticker might be splashed, like on a water bottle or the side of a vehicle during washing.
Stage Three: Submersion for Seconds
Submerging stickers underwater for a few seconds tests for quick, accidental drops into liquids, such as a sticker on a bottle briefly submerged in a sink.
Stage Four: Prolonged Submersion
This stage tests for prolonged exposure to water, simulating stickers on items that might be submerged or left in the rain for an extended period. The aim here is to see if the material degrades over time or if the adhesive strength weakens.
Stage Five: The Rainforest Rumble
The ultimate test of a sticker’s waterproof claim is an exposure to a high-moisture, high-heat environment, like a terrarium or the rainforest. Such conditions push the material to its limit, revealing any issues with adhesion or the material’s ability to endure extreme circumstances.
Lab-Grade Tests for Sticker Material Durability
For small business owners looking for precision in their sticker testing, there are laboratory-grade methods that offer extensive evaluations. The following are a couple of such tests that can be run under more controlled conditions.
Adhesive Strength
This test measures the adhesive force of a sticker under specific conditions. A machine applies increasing force to the sticker until it detaches, allowing for precise calibration and comparison among different materials and adhesives.
Material Integrity
By using specialized machines to stretch, compress, or twist the sticker material, its limits can be determined. These tests reveal the breaking point and the elasticity of the sticker’s material, which can be vitally important in certain applications.
Real World Testing: The Durable Sticker Challenge
While laboratory tests provide essential data, nothing beats real-world testing. The Durable Sticker Challenge involves placing the stickers on items exposed to typical conditions to assess performance over time. From the dashboard of a car to the back of a phone, business owners can run their own experiments by using stickers in the field and evaluating their performance regularly.
Setting the Challenge Parameters
Decide on the duration of the challenge and the specific conditions to which the stickers will be exposed. Photograph the stickers at set intervals to document any changes, and ensure these conditions are consistent for a fair assessment.
Evaluating the Results
At the end of the challenge, review the photographs and notes to determine the effectiveness of the stickers. Look for signs of degradation, loss of adhesion, or changes in color and legibility. This real-world data is invaluable in making informed decisions about the quality of the sticker material.
Ensuring Print Quality Matches Material Durability
A waterproof sticker material is only one piece of the sticker puzzle. High-quality printing is equally critical to the overall durability of the sticker. UV-resistant inks and top coats can extend the life of the design, while the printing process itself can impact the colors and clarity of the sticker. Ensuring that print quality matches the durability of the material is key to a sticker that lasts.
The Impact of Printing Technology on Durability
Different printing technologies can have various effects on the final product’s durability. For example, digital printing is ideal for shorter runs and offers the flexibility to change designs quickly. On the other hand, screen printing provides a more durable and longer-lasting print, suitable for outdoor or high-traffic applications.
The Role of Inks and Coatings
Inks that can resist fading and weathering, such as UV inks, are essential for waterproof stickers. Lamination can further protect the printed image. When considering print quality, it’s important to assess the longevity of the design as well as the material.
Industry Best Practices for Sticker Material Testing
Lastly, to ensure a comprehensive understanding of sticker material durability, it’s valuable to look at industry best practices. Adhering to these practices not only provides a standardized approach to testing but also ensures alignments with regulatory standards, if applicable.
Conducting Regular Material Audits
Regular audits of sticker material, both in-house and from suppliers, can catch issues before stickers hit the market. Simple visual inspections and quick adhesion tests provide early warning signs of potential problems.
Utilizing Environmental Chambers
Environmental chambers simulate a wide range of conditions, from extreme heat to freezing temperatures, enabling thorough testing of sticker materials without needing to run real-world tests.
Partnering with Accredited Laboratories
For thorough, third-party evaluations, businesses can partner with accredited laboratories that specialize in material testing. These experts can offer unbiased reports and advice on how to improve sticker material quality.
Conclusion: The Ultimate Battle-Ready Sticker
To sum it all up, the quest for the ultimate battle-ready sticker is one that requires a multifaceted approach. Understanding sticker material properties, selecting the right tests, and ensuring a match between material and print quality are all crucial steps. While laboratory-grade tests provide precise data, nothing beats real-world performance. By following the principles outlined in this guide, small business owners and marketing professionals can confidently select, test, and deploy waterproof stickers that reflect the endurance and dependability of their brand. Stickers that can weather any storm are not just an investment in marketing; they’re a statement of resilience, quality, and the enduring spirit of innovation.
In the fast-world of branding, where stickers are a challenge and a testament to the risks and rewards of modern marketing, knowing your materials, and how to test them, is the mark of a savvy brand warrior. For those ready to take their marketing strategies to the next level, the time to wage sticker warfare has come. Prepare your arsenal with this guide, and ready the banners of your brand to fly high, in all conditions.
Thanks for visiting https://jihansyakira.com